生産技術部のK・Oにとって「スカイマスターSH15C」のプロジェクトに参画するにあたり、多くのプロジェクト・メンバーは旧知の間柄でありプロジェクトを遂行するうえで不要な緊張はなかったという。逆にプロジェクトに参画することで、普段、製造現場にいるとなかなか見えてこないお客さまの声を聞ける機会はありがたく、情報伝達もスムーズであり、PL会議において、スカイマスターの後継機に求められている期待や要望も肌で感じたという。
K・Oの役割は、設計部門からの要望に対して、製造チームの中で議論を行い合いながら、設計部門と製造部門を繋ぐいわば重要なパイプ役であった。長らく製造部門で経験を積みながら、本プロジェクトでは生産技術部門のプロジェクト・リーダーとして抜擢されたK・Oは、ものづくりの現場に精通した生産技術職としての大きな期待が掛けられていた。
「今回のプロジェクトでは、組み立ての工程に入る前に製造チームを呼んで会議したことがとても良かった。図面の構想がある程度固まってしまうと、そこから変更するのが難しい。その前に、製造側の意見を取り入れることがとても重要だと考えていました。また、通常の進め方では生産技術・製造部にまで届きにくい、開発プロセスが見えてくることで、進捗状況によってリアルタイムに生産工程の見直しやスケジュール感覚などを共有することができ、スムーズな意思決定につながった」とK・Oは語る。
構想段階から時間をかけて考えられたSH15Cの製造には、とにかく「作るための時間の確保」に追われたという。完成までの期日は決まっており、限られた時間の中でアイチコーポレーションの品質基準をクリアする車両を完成させなければならない。何度も試作機をつくり、品質を確かめ、また試作段階に戻っては部品を一つずつ生産していく。その積み重ねだったという。品質の担保と迫る期限の中、K・O率いる生産技術・製造チームは一丸となってこの課題に取り組んだ。
manufacturing生産 編
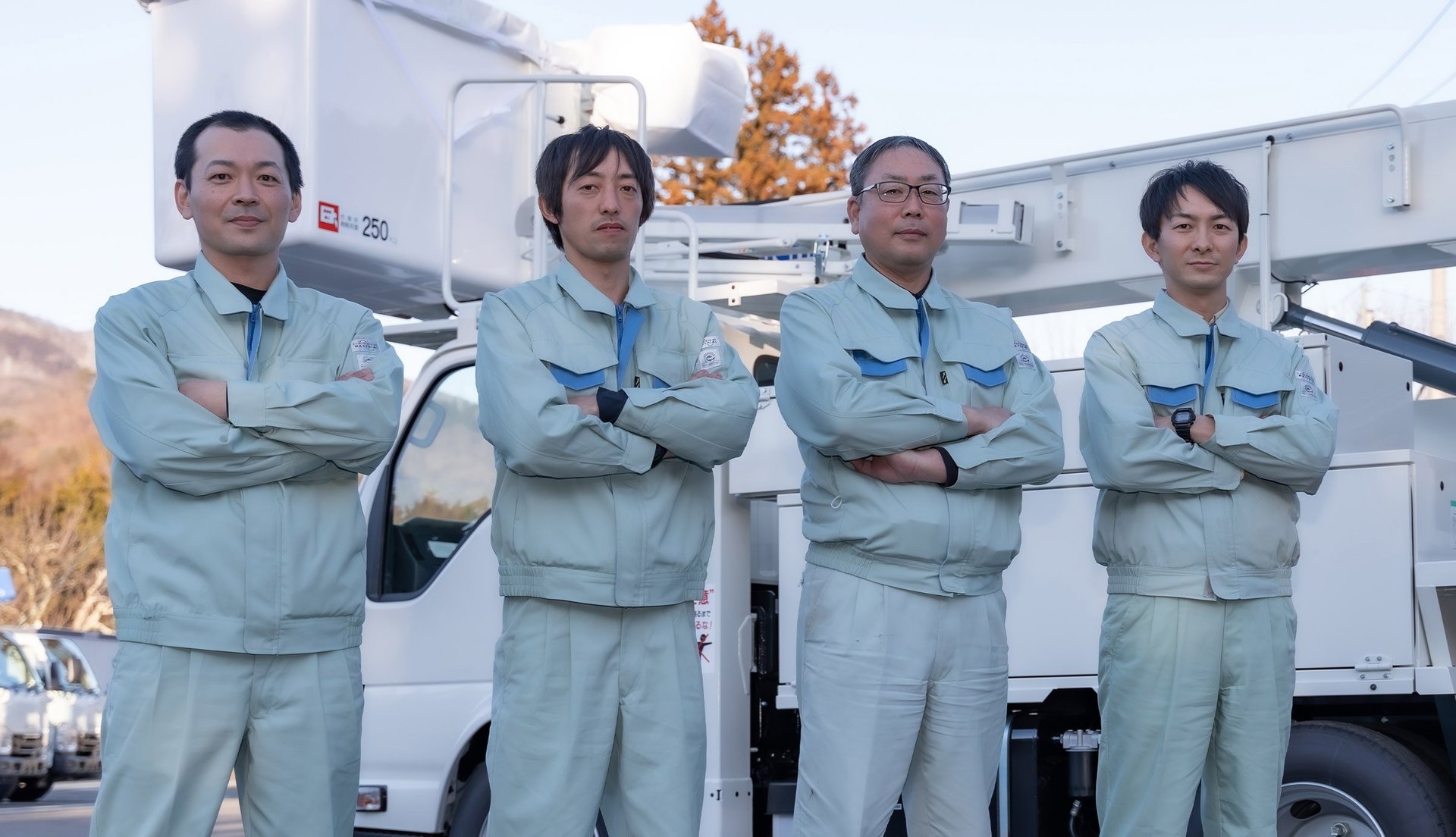
03Project 理想とした車両が姿を現し動きだす
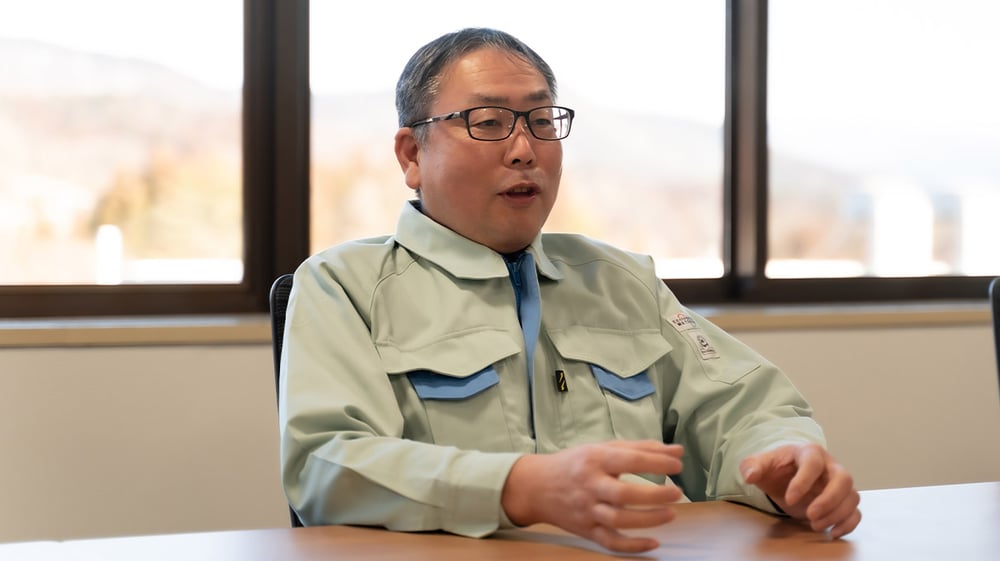
K・O
生産技術 新治生産技術課
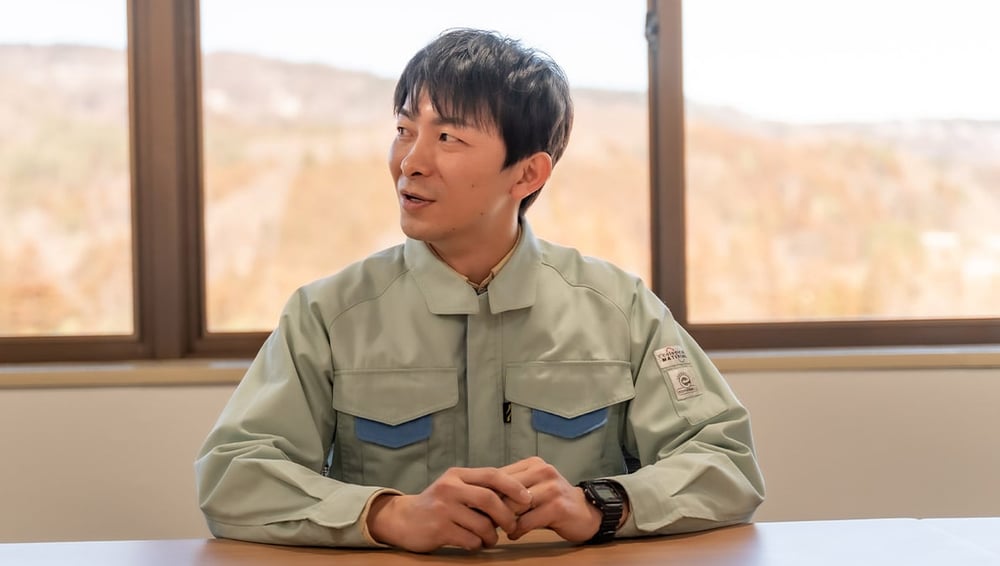
T・H
生産技術 新治生産技術課
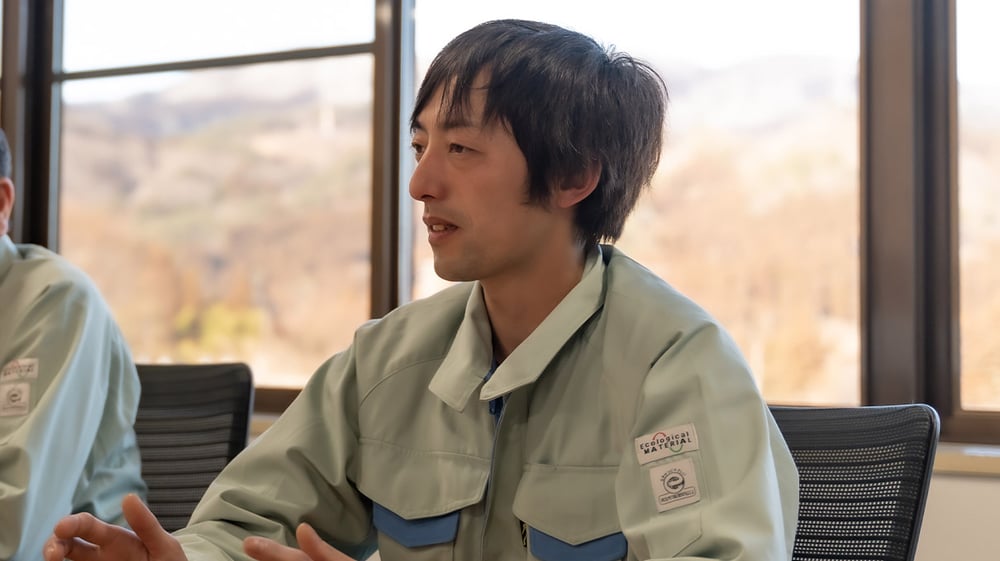
S・S
新治製造部 製造一課
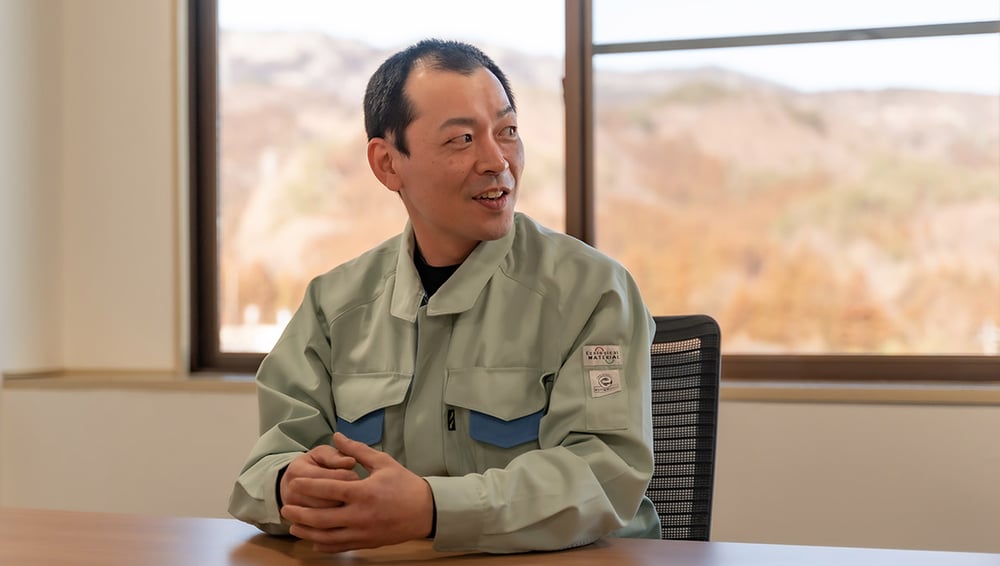
M・I
新治製造部 製造一課
社運を掛けた一大プロジェクト
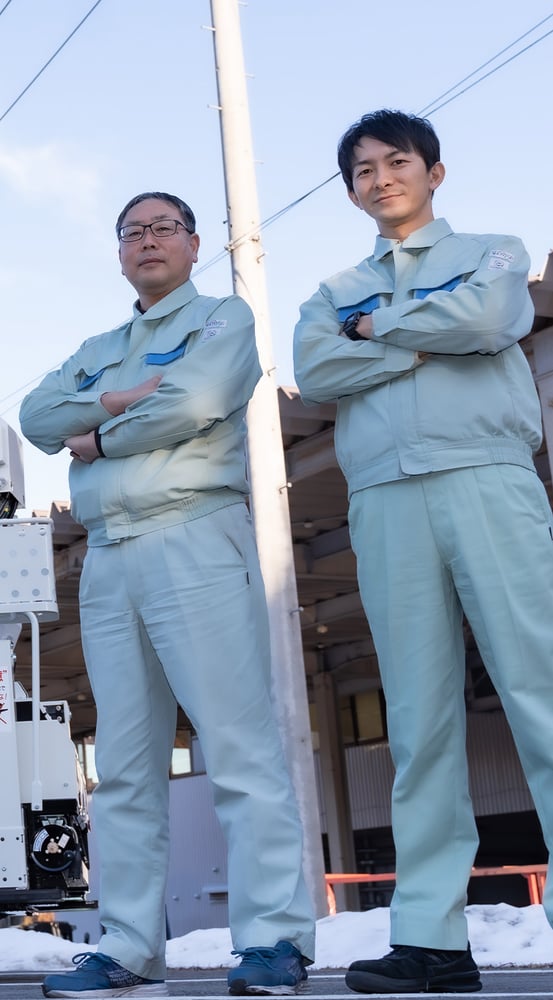
「新しい製造技術」を追い求めて
実は製造部は、スカイマスターSH15シリーズの初代のSH15Aから組み立てに携わってきた歴史がある。だからこそ、各車両の違いが手に取るようにわかるのだという。とくにスカイマスターSHシリーズは、アイチコーポレーションの中でもグレードが高く、絶縁機能を備えた特殊車両であること以外にも、他の車両と比べてオプションが豊富であり、オプションの組み合わせによっていくつもの組み立てパターンが存在する特別な特徴を持っている車両であり印象深いシリーズなのだという。
組み立ての際にも非常に気を使う。高所作業車としてブームがあるが、ブームに少しでも傷がつけば全て交換になってしまう。「組み立てには最新の注意を払う」と製造部のS・SとM・Iは語った。
製造工程では当然、生産効率も考えなければならない。組み立ては工場内の定められたラインで行われるため1工程あたりの作業時間は予め決められており、それを厳守する必要がある。ライン全体が動いているため、どこかの工程で規定の時間を過ぎてしまった場合、ライン全体が止まってしまうことになり、製造スピードを大きく遅らせてしまうことになる。そのためにも製品や部品を吊り下げたり加工をしやすくしたりする「治具(治工具)」をいかに製品に合わせて早く準備できるかは、製造部としても重要な課題だという。
今回のプロジェクトでは、生産技術/製造を代表するK・OがPL会議に参加することで製造部の声も会議に届けられる。会議で話し合われた仕様をベースに、生産技術は試作の段階からSH15Cに見合う治具を作製することで、製造チームとの連携や量産化フェーズへのスムーズな移行が可能になった。
本来であれば、治具は製品がライン上に流れてきた段階でつくられるもの。しかし、製品によっては合わないものもあり、そのたびにラインを止めていては生産効率は大幅に損なわれてしまう。だからこそ、試作の段階から治具をつくれたことは、生産性の向上に大きく寄与したのだという。
これは「各セクションが参加するPL会議」が、製造現場にまで影響を及ぼした好例だった。
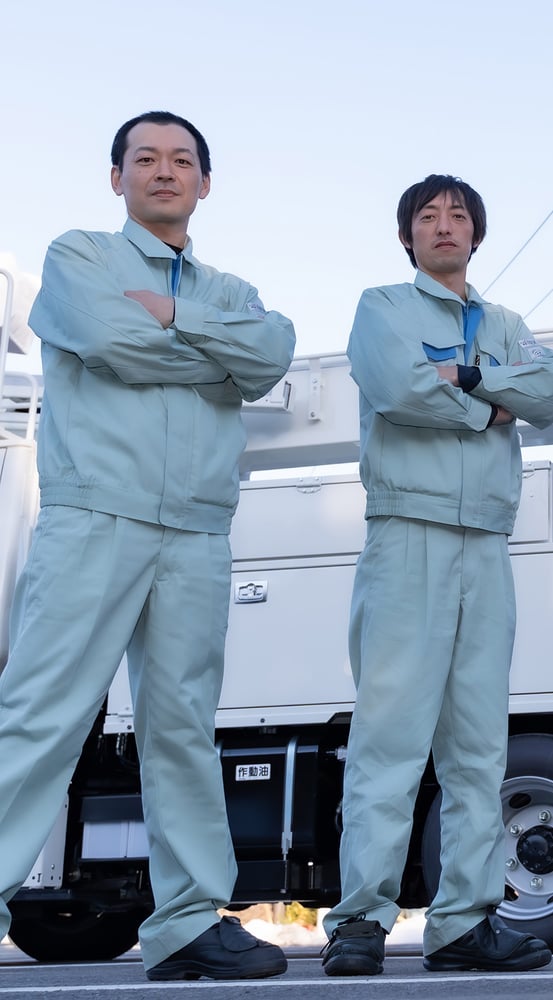
製造現場における「デジタル化」で
製造を加速させる
生産技術/製造チームにおいては、納期までの短さに悩まされた。設計から図面が完成して仕掛かり、試作を作るのだが、コンセプト決めや設計書を作成するタイムラグがあるために、どうしても試作機を製造する時間が短くなってしまう。しかし、納期は伸ばせない。待ったなしの状態でスムーズに工程を進めるためには、現場で組んでもらうための作業指示をいかに分かりやすく、素早く共有する工夫がとても重要だったという。
3Dの図面であれば、新しい製品であっても立体的に把握することができ、直感的にイメージを掴める。今では浸透している3D図面だったが、開発プロジェクト当時は、部内は3D図面の導入期であり、慣れ親しんだ平面の図面から3D図面に慣れる努力も必要だったという。2Dの図面を元に作業指示を作成する場合、図面自体を切り貼りしながら指示を出す一方で、3Dはタブレットなどで見やすい角度にCADデータの視点を変更しながら指示に落とし込むことができるが、当初はその扱いにも慣れておらず、加工するにも手間が掛かったという。
また、今回のプロジェクトから「作業ナビ」というデジタル・シフトも実施したという。製造チームの一人ひとりにタブレットが手渡され、手元で図面が確認できるようになった。従来は、組み立てにあたって製造チームの一人ひとりに専用の本棚が置かれ、そこで紙の図面を確認し、組み立ての現場と本棚を行き来するような流れであった。こうした時間もデジタルシフトによって効率化を行い、全体の生産性を向上させていったという。
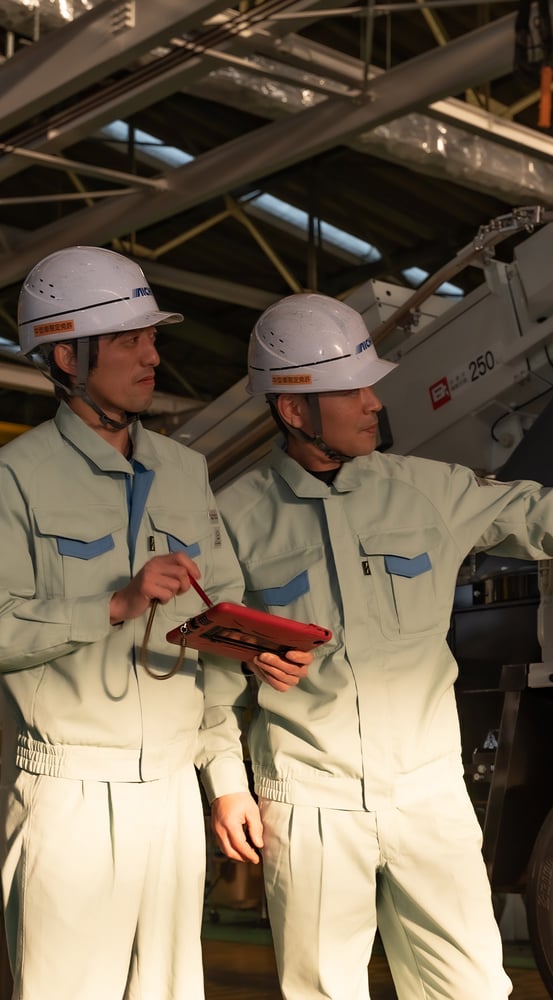
理想と現実の狭間
設計段階では見えてこなかった
課題に立ち向かう
試作機を組み立てる段階では、問題点や改善点をリストアップして、設計・生産技術・製造と話を詰めていく。議題は数百に上るほど細部に至るまでさまざまな課題が浮かび上がってきた。
どれほど設計技術が発展しても、実際に組み立てる段階にならないと見えてこない課題がある。それは3D図面が浸透した現在においても変わらない。
たとえば、M・Iが「とても苦労した」と語ったのはエンジンユニット周りだった。下層部の狭い部分、ホースと電気ハーネスが通っている中に溶接物をつける指示があった。溶接すること自体、現場からは難色を示されるほど高度な技術だが、そこにホースと電気ハーネスを通したいという。どのような治具を作ればいいか悩み続けたという。設計の「こうしたい」と、製造の「どうすれば可能か」がぶつかる瞬間でもあった。これはエンジンユニットだけではなく、試作の段階で何度も経験したことだった。こうしたいくつもの課題を、生産技術の知恵と製造の技術によってクリアしていった。
「設計図だけではわからないことが、必ず現場では出てくる」とK・Oは語る。2Dの図面から、3Dの図面へと変更になり、また、生産技術としてK・Oが会議に参加することで現場の声を反映させやすくなったとはいえ、現実に部品を組み立てていけば必ず想定外は起こり得る。そのたびに現場で頭を悩ませ、会議を重ねながら、理想の形を現実のものとするために努力を続けていった。
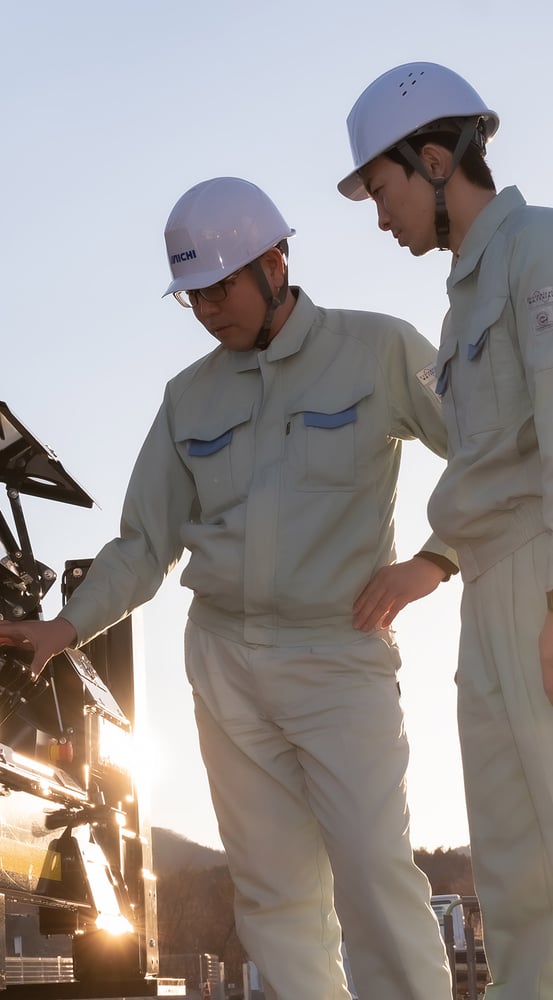
新たな製品の特徴に対応するために
スカイマスターSH15Cの目玉として開発された無段階アウトリガーは、基本設計はSH15Bを踏襲しながらもソフトウェアの制御方法が変わりデータの扱う量も飛躍的に増えたことで、配線周りが複雑になり、製造時には経路を塞がないようにケーブルを引き回すためさまざまな工夫を重ねた。
何より困難だったのは、サブフレームの形状だ。試作段階でも何度も変更を重ねるうちにSH15Bと比べて、溶接の長さが数メートルも伸びてしまったのだ。設計当初では強度を維持するためには「溶接を一回すれば良い」という計算だったが、実際には、品質を担保するために二回の溶接をしなければならず、その部分の工数が増えたのだという。
また、新しい製造手法を実施する際には品質のチェックも慎重に行う必要がある。溶接したサブフレームの変形の傾向を把握するため、何度も何度も試作を繰り返し、最終的に品質を安定させるために数ヶ月を要したという。
また、下部操作装置(マルチインフォメーションディスプレイ)も、今回のスカイマスターSH15Cの大きな特徴だ。これまで様々な特殊車両を組み立ててきたM・Iも「他の車両で見たことのない装備。設計のこだわりを感じる」と評した。これまでのアイチコーポレーションの長い歴史の中でも初めての、デジタル表示で車両の傾きや状況を表現する画期的なシステムであり、製造チームから見ても外観の良さを感じるデザインだと語った。
一方で、その配線の引き回しには苦慮したという。ただでさえ軽量化を目指し省スペースな構造となった車体に、どのようにすれば干渉せず配線を通せるのか。すべてを組み上げてから新たに見えてきた課題もあり、一進一退を繰り返しながら、部品一つ一つを着実に完成させていった。
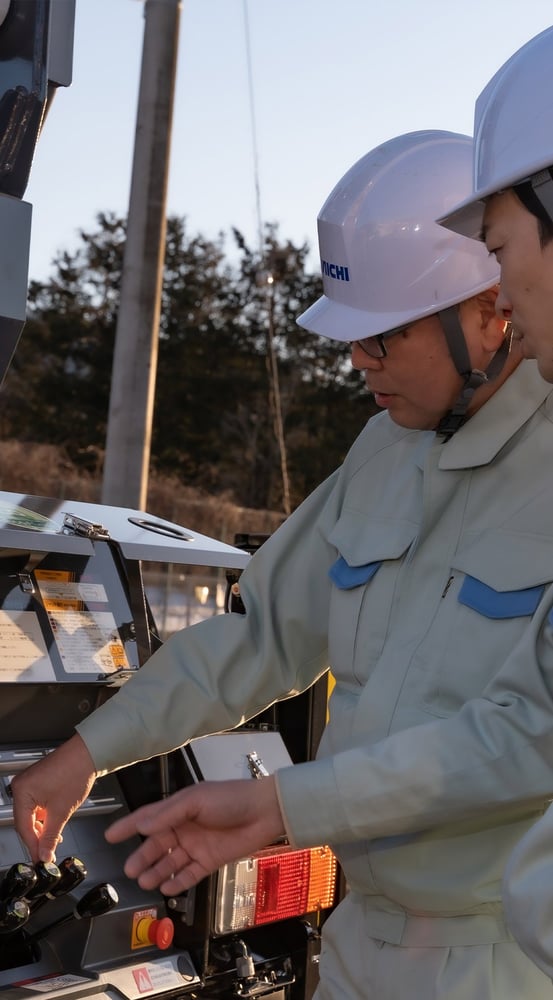
完成品を前に蘇る開発の日々
プロジェクトを振り返って
「試作時の製造は、製造課に任せれば1から10まで、良いところから悪いところまで抽出してくれる」という言葉でK・Oは製造チームへの信頼を語った。現場で誰よりも長く実機に触れている彼らだからこそ、新しい部品であってもすぐに理解し、より良い製品にするためのアイデアが生まれてくる。生産技術と製造現場、双方の信頼なくしてスムーズでスピーディな量産化の確立は不可能だ。
M・Iは「生産技術において、製造現場・設計、生産技術の声をすべて聴けた上で、組み立てを行えたことが、自分の成長につながった」と語った。S・Sは「今回が私自身のキャリアで初めての、大きなプロジェクトへの参画だったが、社内のレスポンスの良さを感じた。他部署とのチームワークを実感しましたね」。T・Hは「量産型の開発には初めて参画したが、現場でのコミュニケーションを沢山取ることで、これまで知らなかったような知識も身につき、今後の開発にも役立たせることができる。成長したと感じた」と話した。
一方で、プロジェクト・リーダーであるK・Oにとっても今回のスカイマスターSH15Cは初めての新規開発プロジェクトへの参画となった。「大きな新規開発案件のプロセスを一から経験できたことが大きかった。今現在もPL会議のときのように各セクションが一体となって開発するようなプロジェクトが存在し、何機種かは同様なやり方で開発を進めている。今日までスタート当初と同じメンバーで続けてこられたのは、このプロジェクトを通して良い関係が築けた結果だと思う」と語った。
T・Fは、完成したスカイマスターSH15Cが社内の待機場に置いてあるのを見上げ、ようやく安堵した。開発における苦悩の日々が思い返され、感動すら覚えた。
「現場に寄り添う”空気”のような、いて当たり前の存在になりたい」次世代のスカイマスターSH15Cもそれは同じ。これからも現場の安全を見守り、なくてはならない高所作業車として活躍していく。
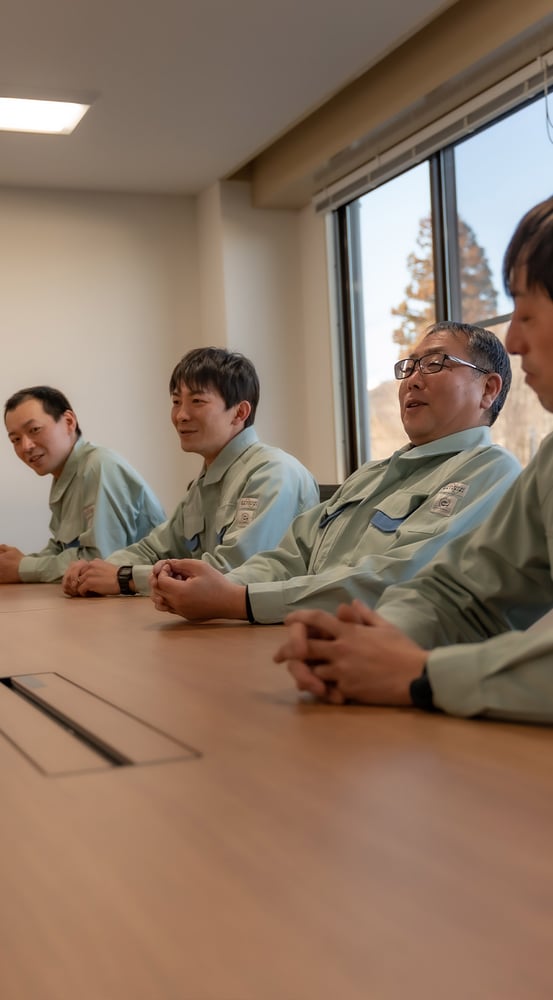